Stages of Drying
An examination of the physical stages in the drying process will reveal why the action of the Littleford Ploughshare Vacuum Dryer is so efficient.
Materials go through several physical stages during the drying process – Paste, Granule, and Powder. During the early portion of the Paste Stage (see Figures 1 and 2), the product is a thickening slurry which is readily put into turbulence by the action of the plows. This is because the Littleford Ploughshare Dryer has been designed and engineered to achieve the critical Froude number (the point at which the plows force the batch into turbulence and thus maximize the heat transfer capability of the dryer), as shown in Figure 3. the Littleford Ploughshare Dryer’s attainment of the critical Froude number enables fast, efficient transfer of the BTU’s required to satisfy the latent heat of vaporization, thus generating a much shorter drying cycle.
Conventional dryers do not begin to achieve Littleford drying rates, even in this Liquid Stage of the drying curve where drying is most easily accomplished. Figure 4 compares the heat transfer coefficients attainable in several dryers. As can be seen, the Littleford Ploughshare Dryer exhibits superior heat transfer coefficients, often two or three times higher than those of a ribbon or paddle dryer. In the case of tumble or tray dryers, the Littleford Ploughshare Dryer can provide coefficients ten times higher.
As the slurry thickens at the end of the Paste State (end of the constant rate period), the batch thickens to a mud-like consistency, which in conventional dryers causes the batch to ball or cake. This makes drying exceedingly difficult, since moisture (volatiles) must migrate from inside through capillaries to the particle surface before it can be flashed off. This point on the drying curve is where the limited drying rate of conventional dryers gets even worse, as internal particle drying replaces efficient external drying.
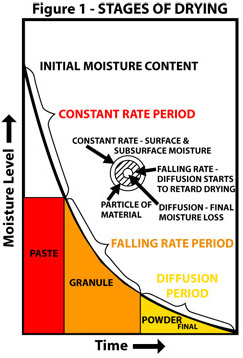 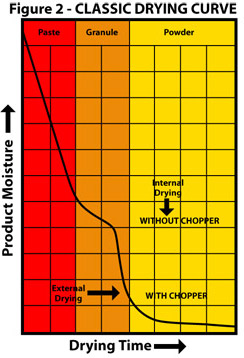
In the Granule Stage, Littleford Ploughshare Dryers, utilizing both the action of the turbulent plows and the high shear choppers, reduce the forming lumps to smaller granules, thus exposing large amounts of new surface area for drying. Choppers are high-speed (3600 RPM) impact devices composed of four or more blades mounted upon the rotating shafts of independently operated motors. The chopper action allows the faster external drying mechanism to remain in effect, thus shortening the drying time. As seen in Figure 2, the slower internal drying rate caused by the formation of lumps is driven back to the faster external rate by the action of the chopper on the lumps.
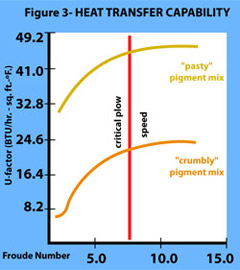 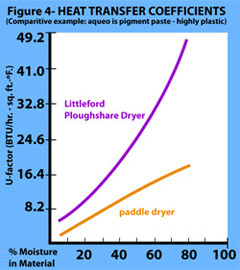
As the product moves from the Granule to the Powder Stage, continued use of the high shear chopper will break the drying granules into a fine powder.
Depending upon the friability of the lumps, use of the choppers may eliminate the need for further milling of the dried product.
In summary, the efficiency of the Littleford Ploughshare Dryers, due to the turbulent action of he plows combined with the high shear dispersive action of its choppers, generates much shorter drying cycles compared to conventional equipment. Shorter cycles means not only less cost in man-hours and energy, but also less capital cost, since the processor can use the Littleford Ploughshare Dryer many more cycles per day. 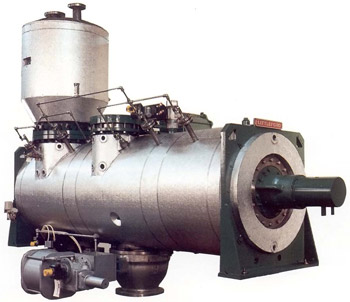 |